Biodegradable sneakers constructed using no glues or adhesives accommodating end-of-life waste management by being able to be disassembled and returned to the earth.
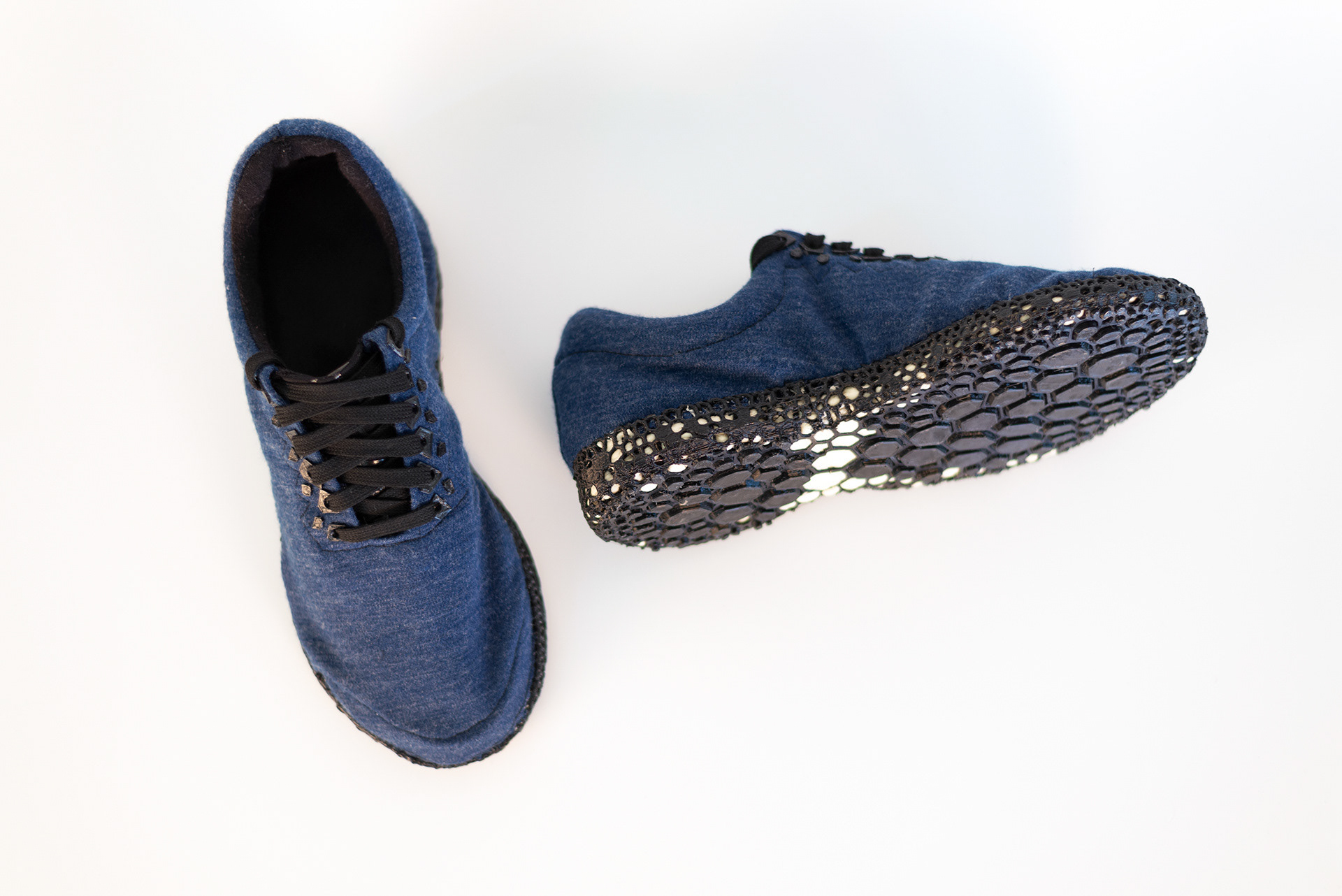
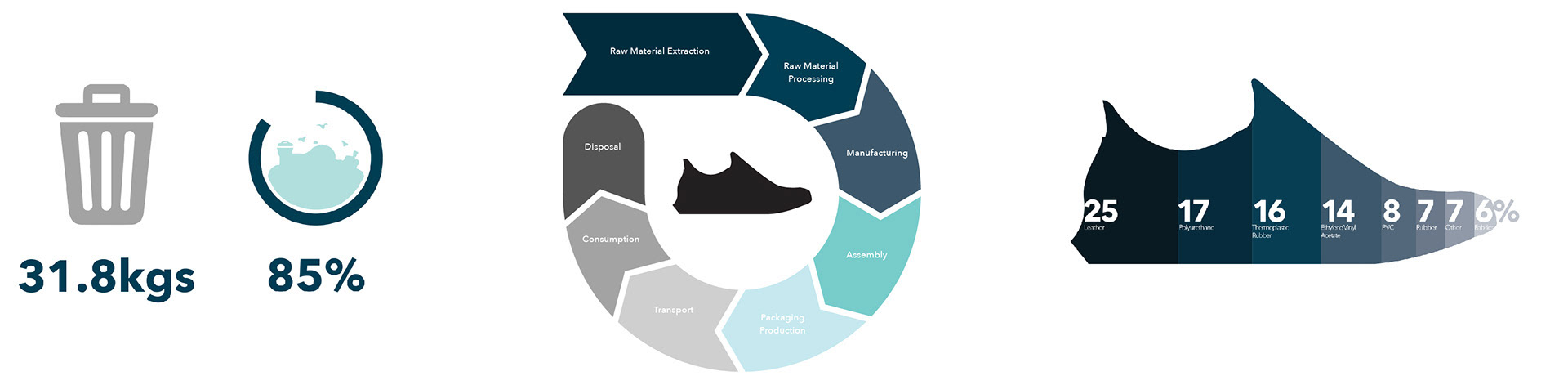
On average each person throws out 31.8kgs of clothing and shoes per year. With 85% heading straight to landfills there needs to be an alternative to the current shoe materials to break the shoe life line.

Using the US market to forecast which shoe styles are growing and targeting Athletic footwear or sneakers. Studies are showing the production and exportation of footwear declining suggesting consumers are valuing locally made ethical goods.
Material Prototyping
Creating biodegradable materials using DIY methods. Using Nature as a partner in the design process to find new material alternatives.

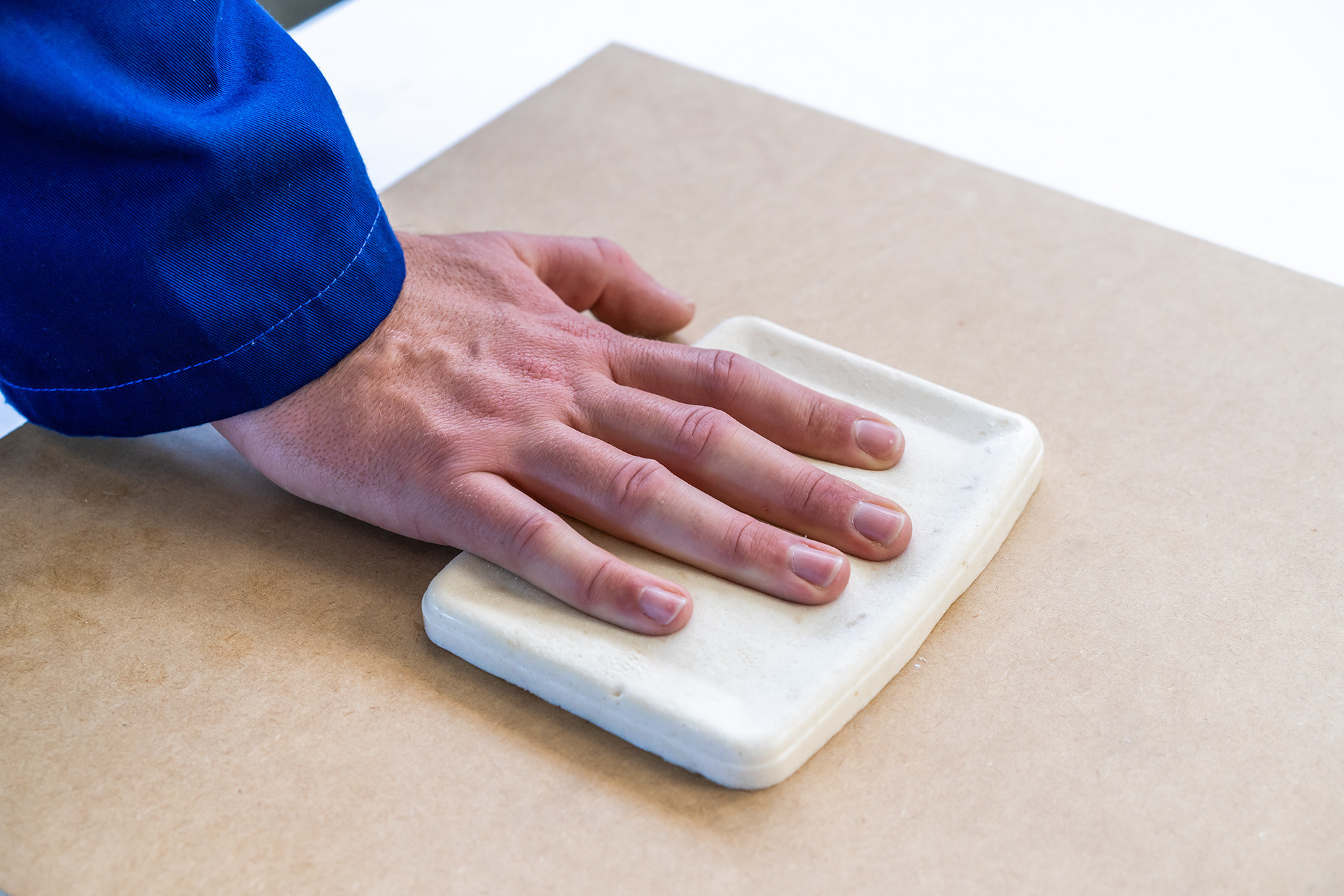
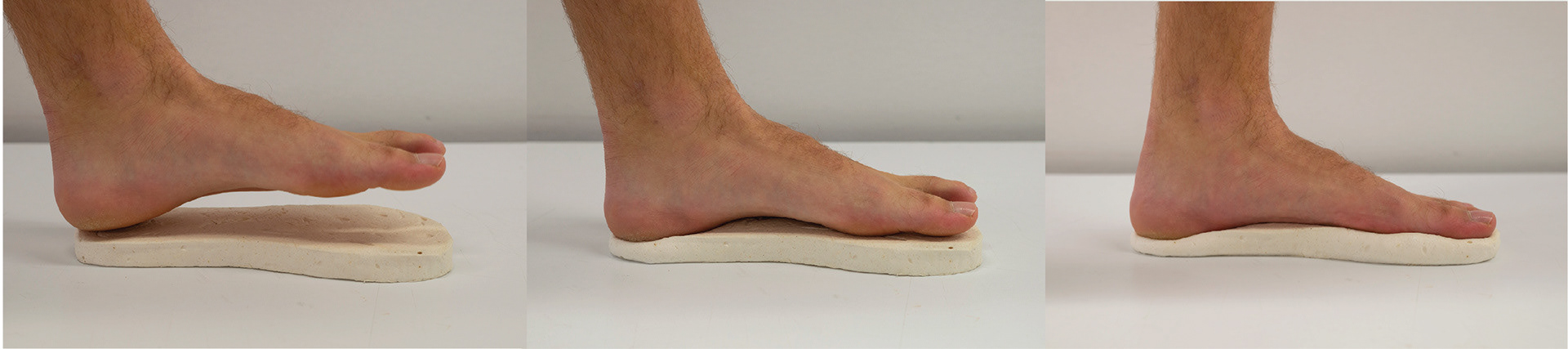
Successfully created a 100% biodegradable foam to be used to replace polyurethane foam in the midsole.
Concept Generation
Design a cage like structure to encase the midsole, this structure can double as the attachment feature so that the sole can be stitched on to avoid using adhesives.
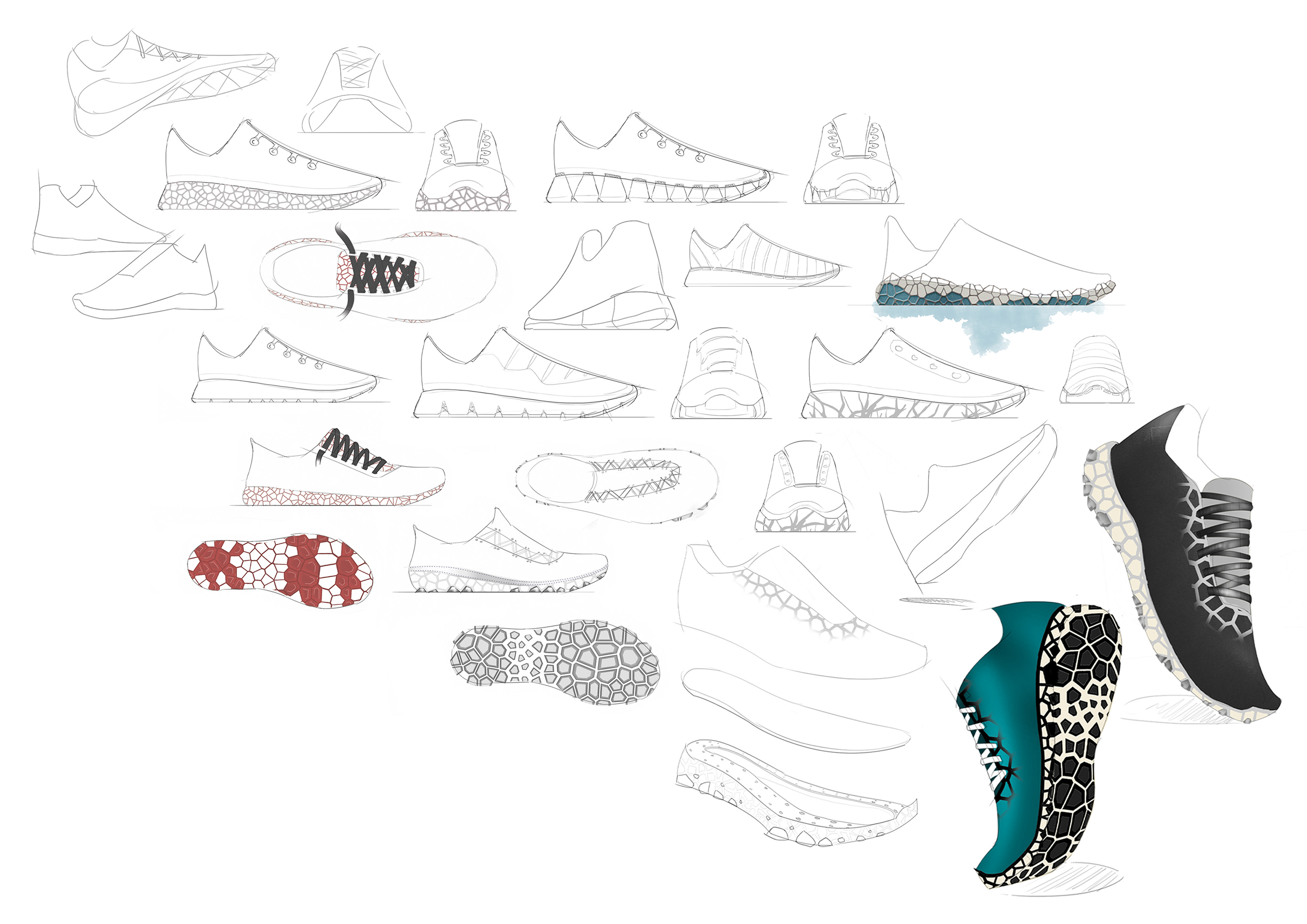
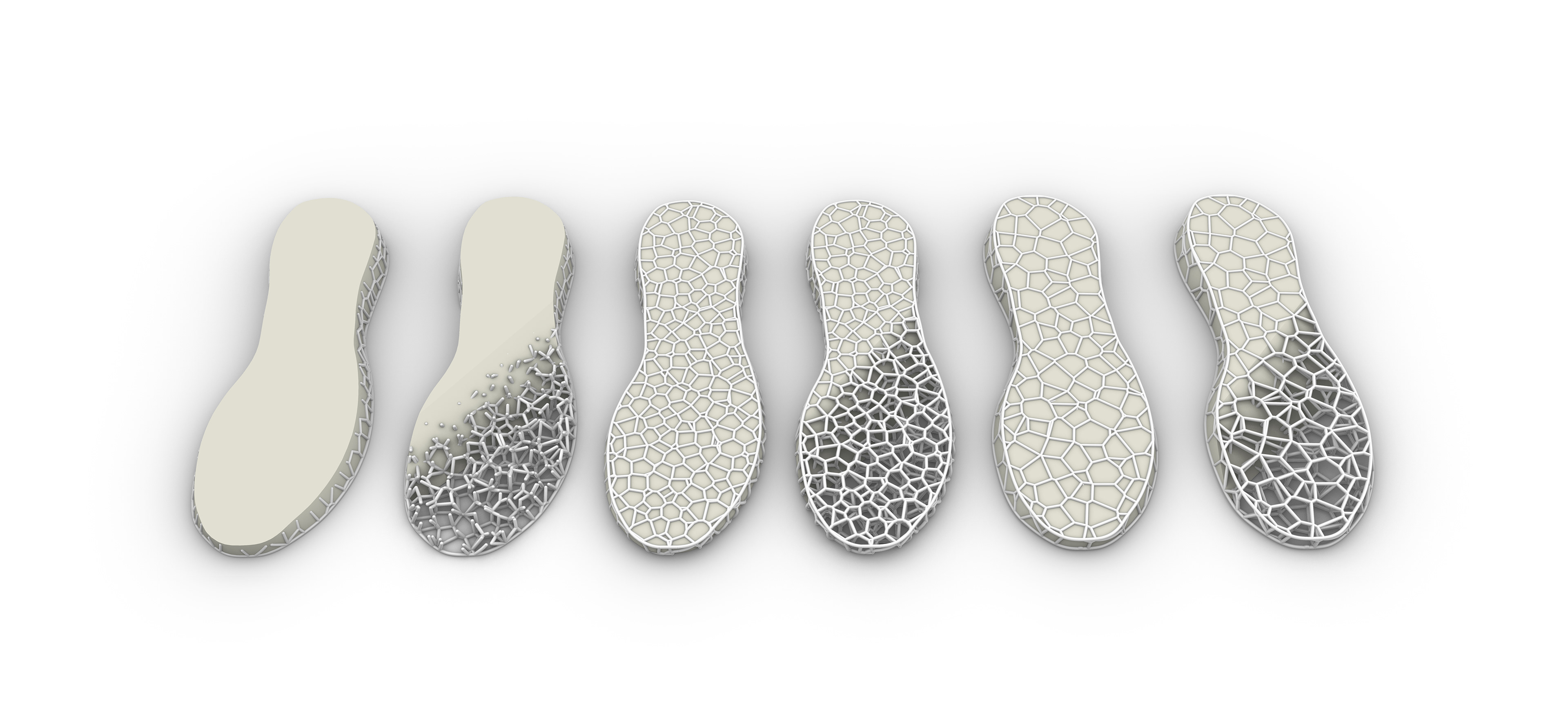
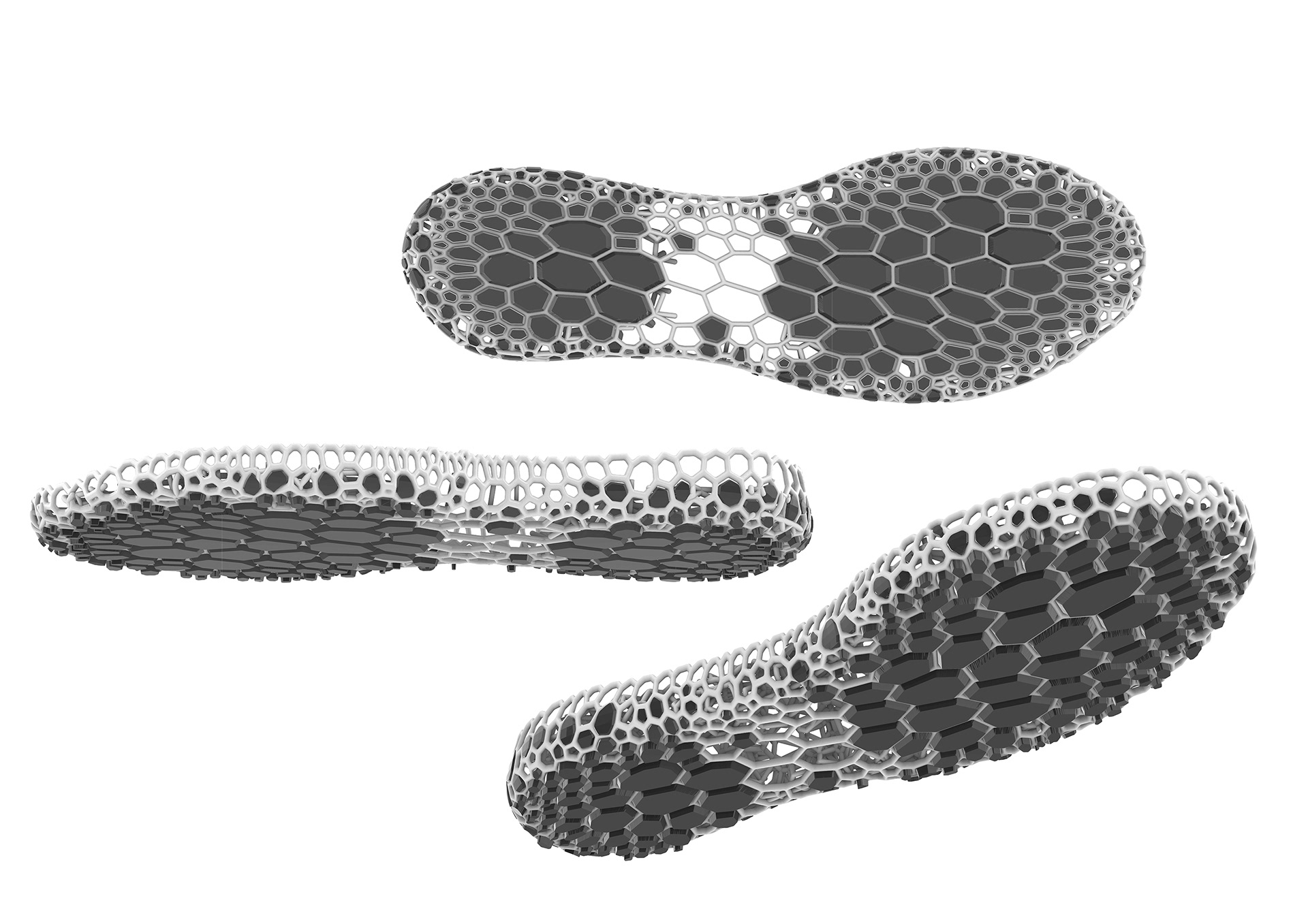
Keeping up with current sneakers by scanning the foot and creating a 3D printed midsole and sole structure to be filled with foam. This way the midsole meets the force distribution and support needs of the individual foot. Created using Rhino partnered with grasshopper.
Prototyping
3D printed offered the opportunity to create custome sole designs that can be printed using biodegradable filamnet. This challenges the traditional footwear manufacturing and allows footwear to be printed locally and saving on exporting resources.
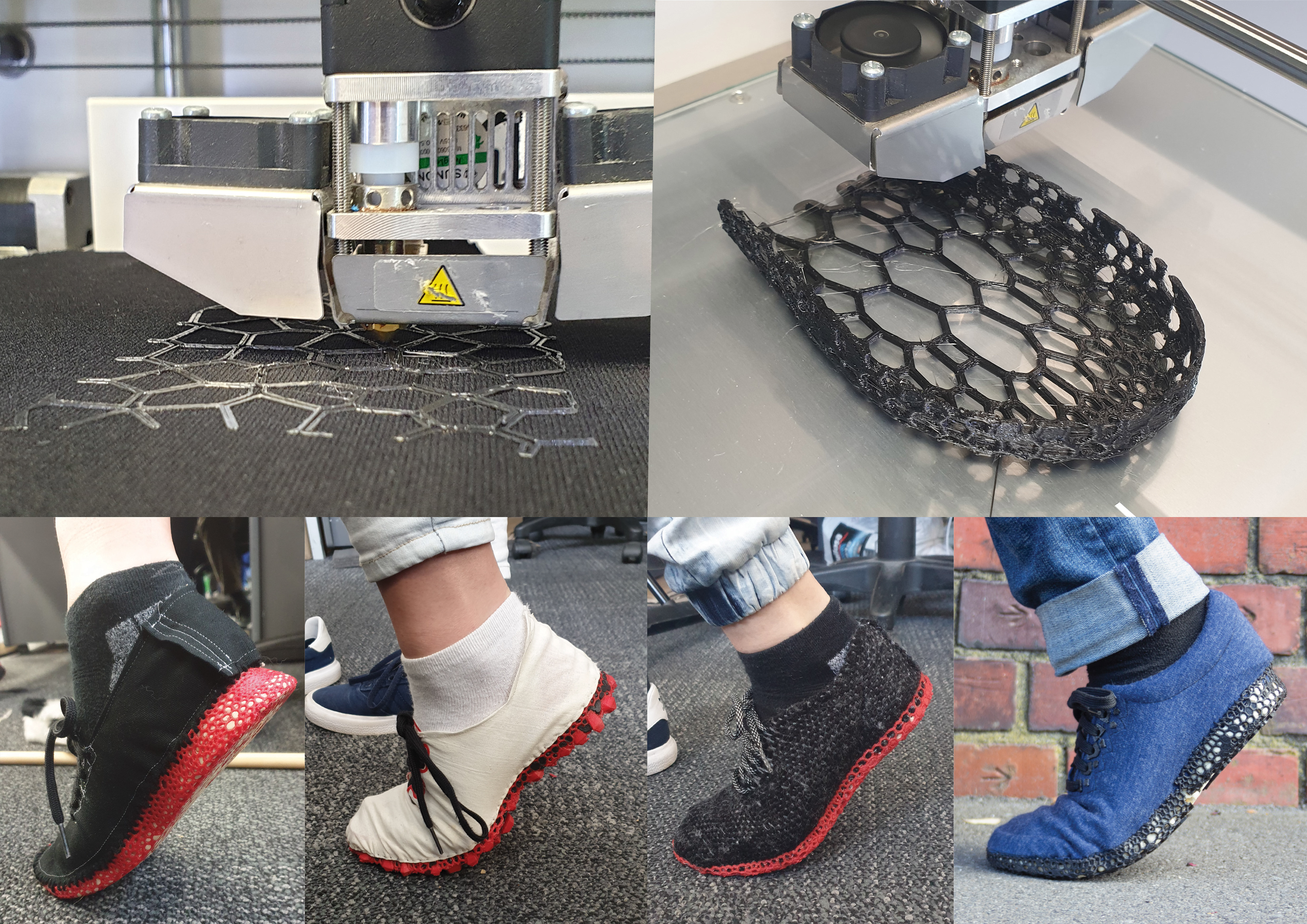
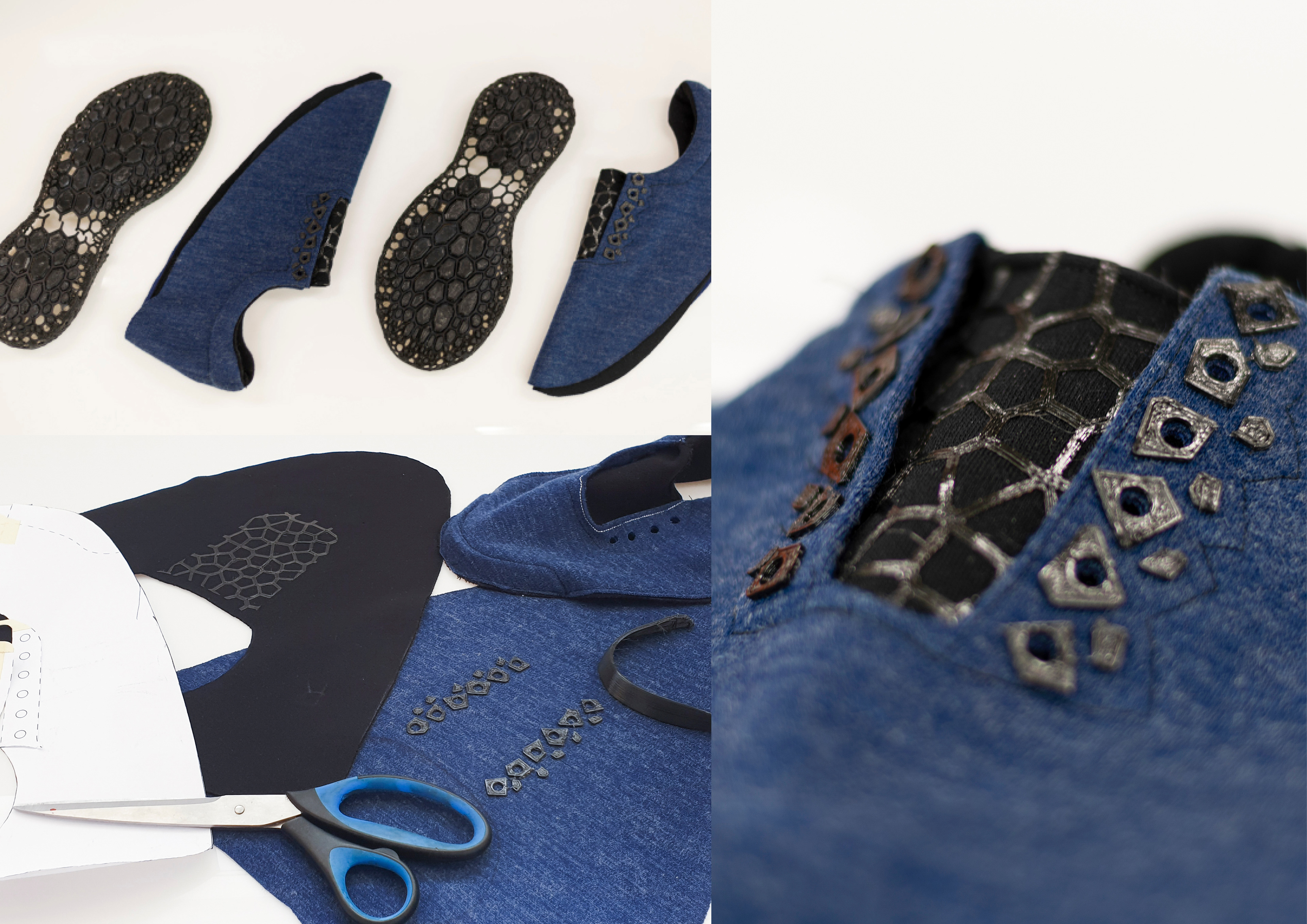
Final Design
Constructed using biodegradable 3D print filament, merino wool, bio foam and linen, the Voronoi Runner uses no glues in construction so that the shoe can be dissembled and composted separately at the end of its useful life.
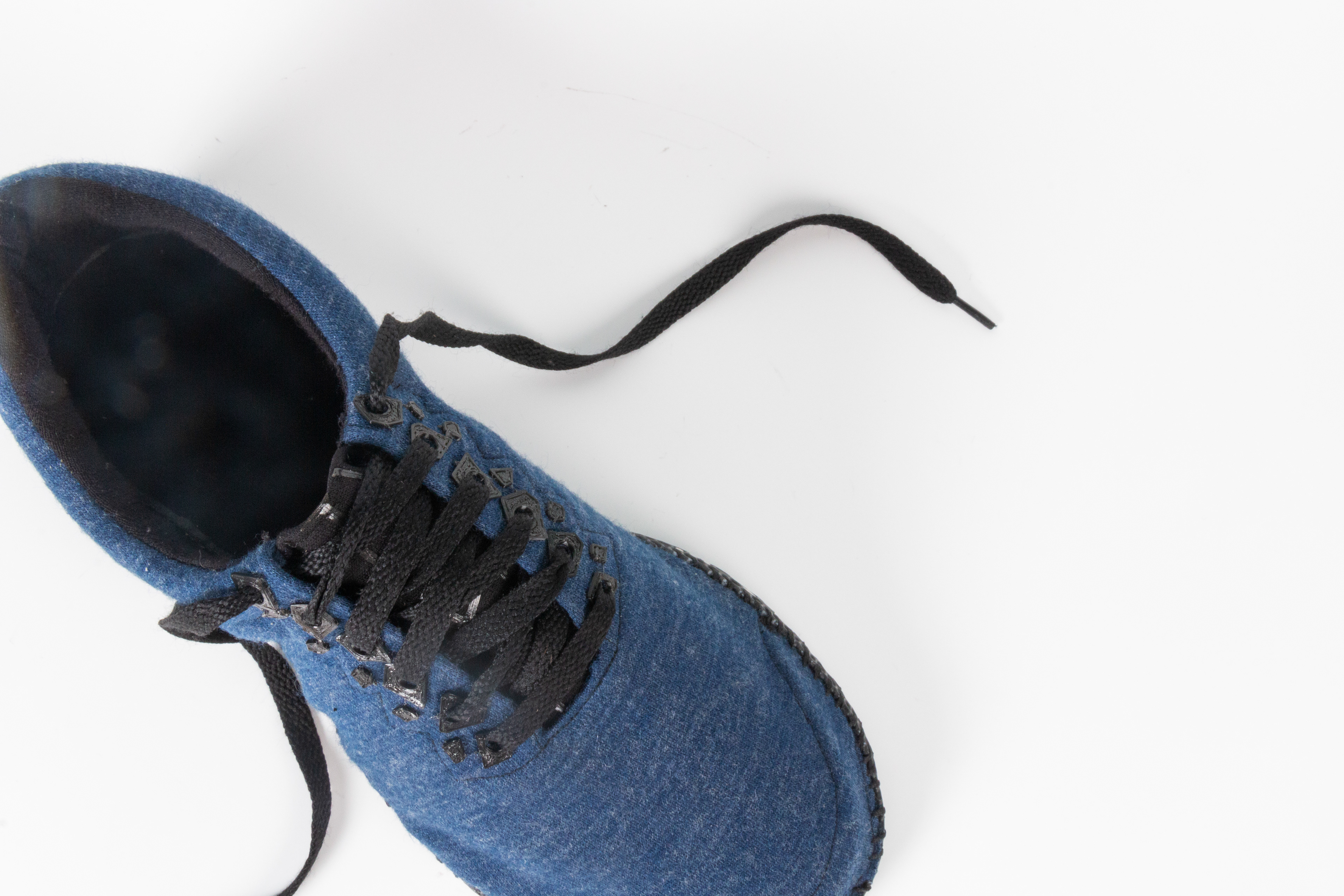
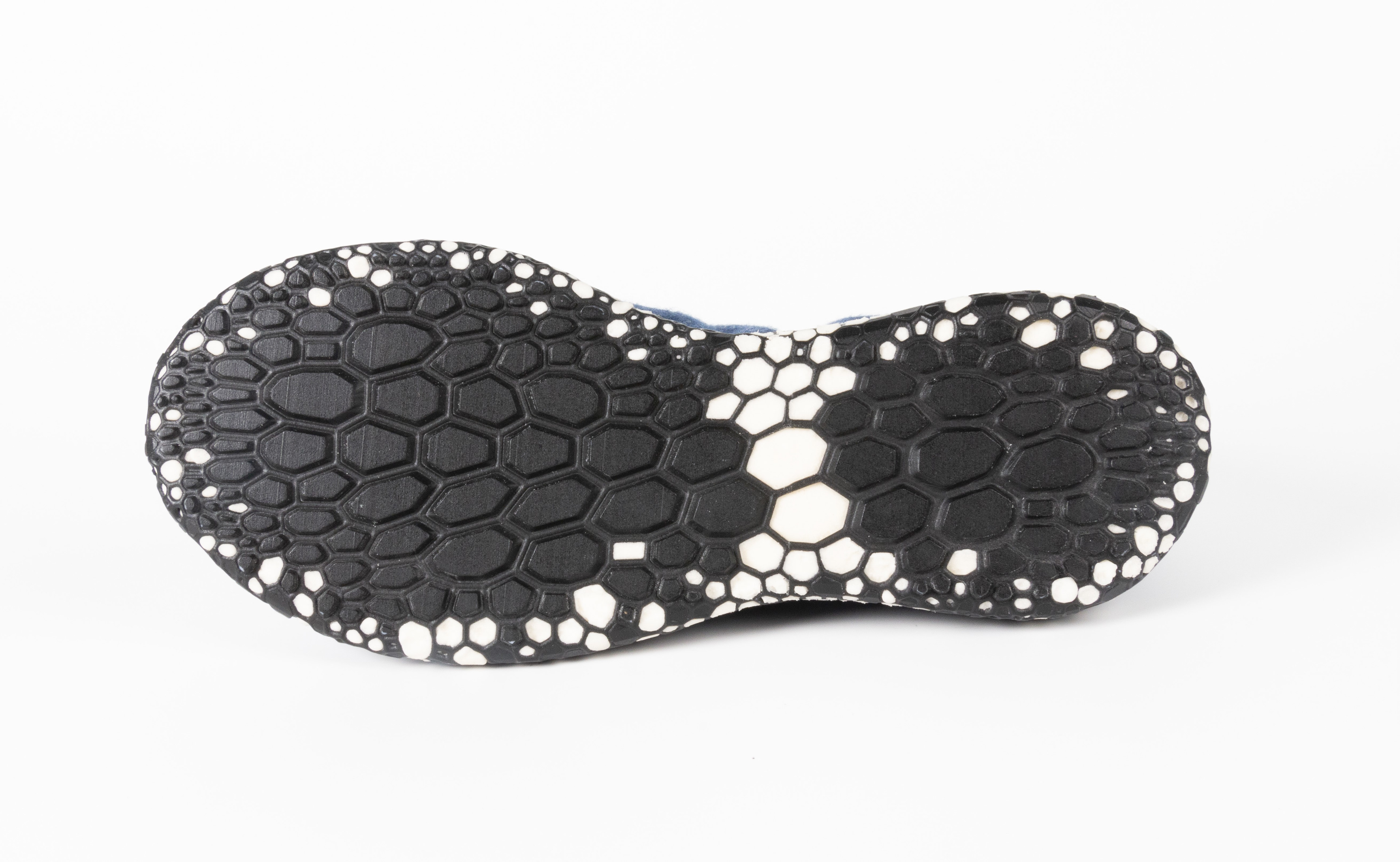
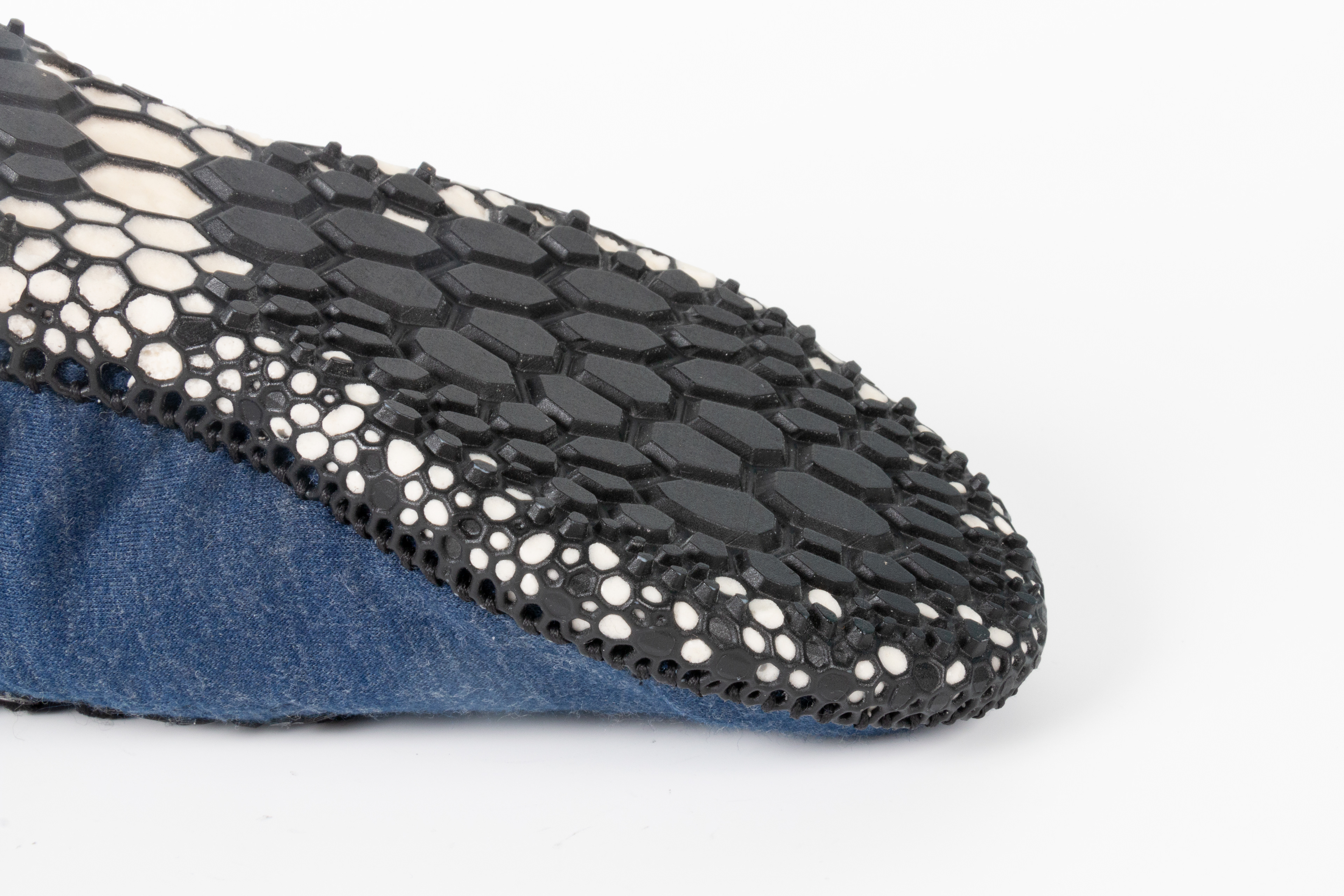
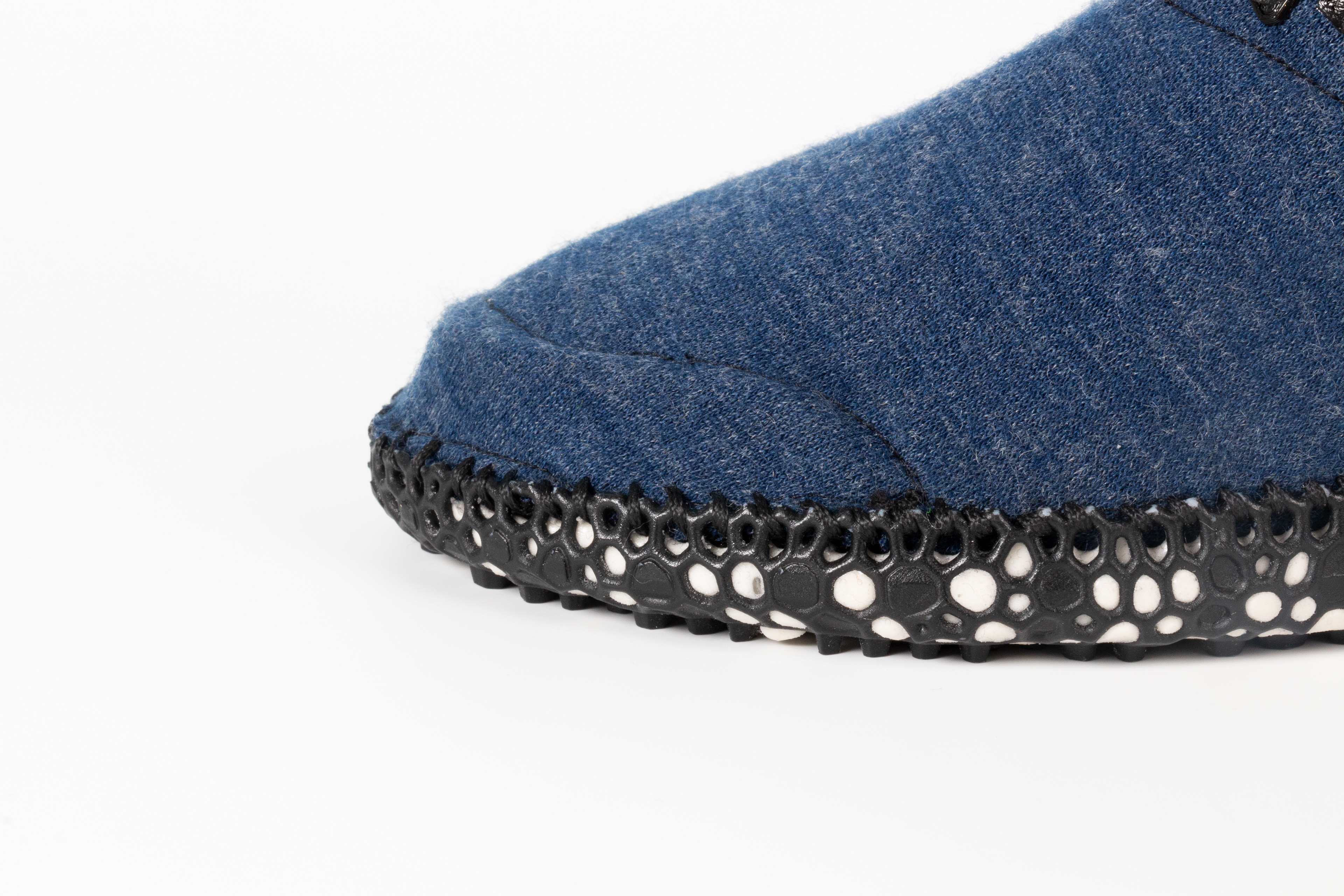
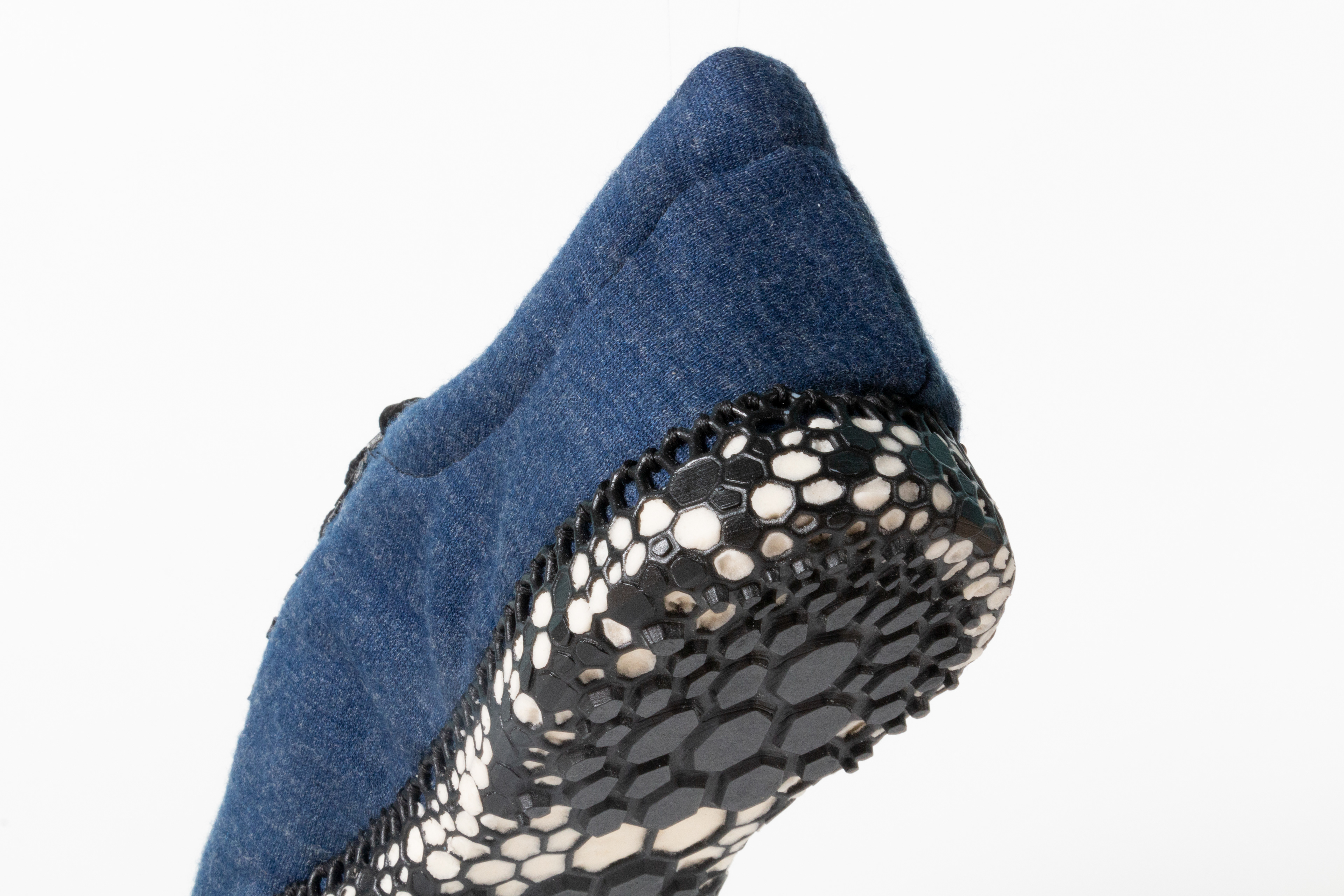
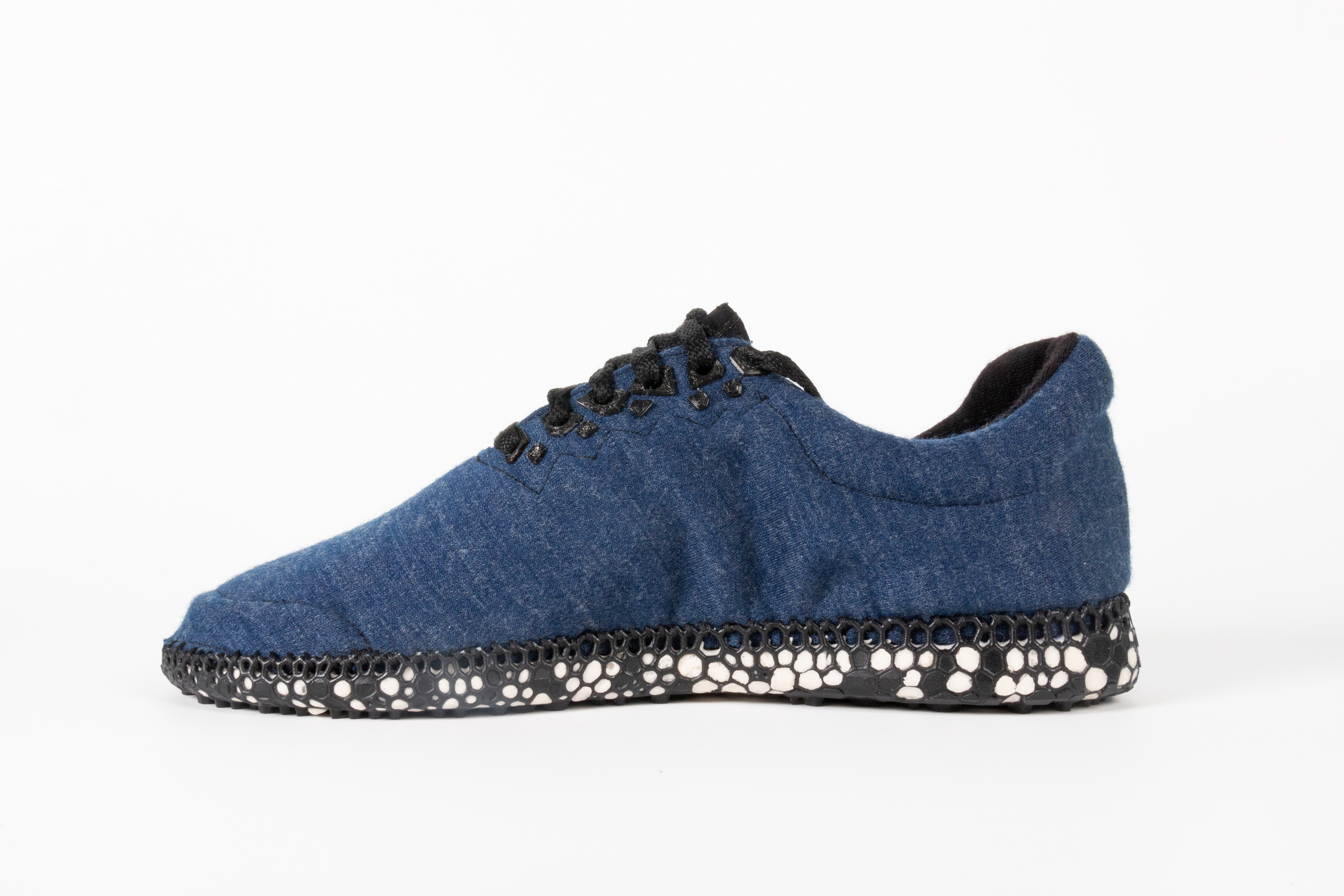
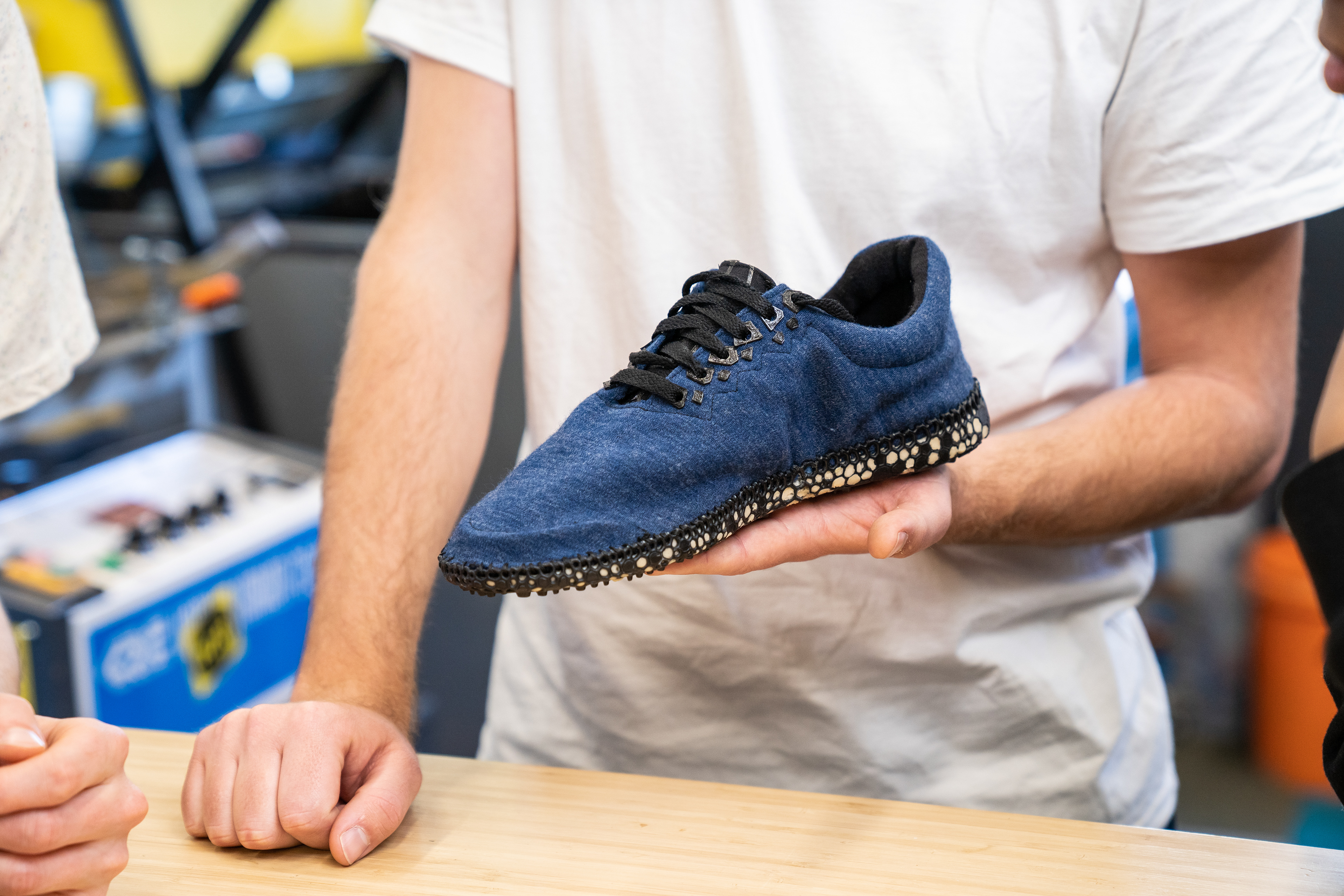
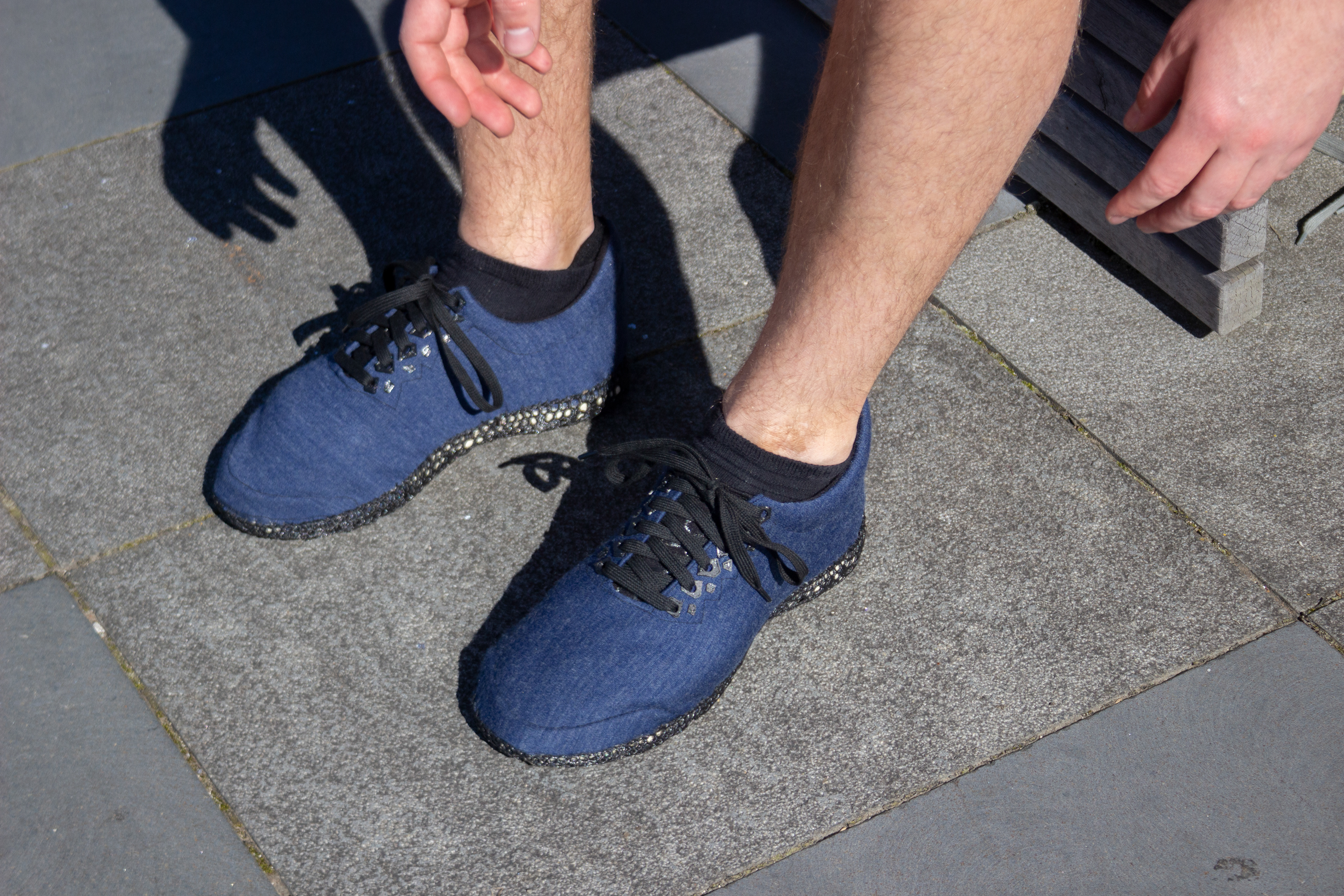
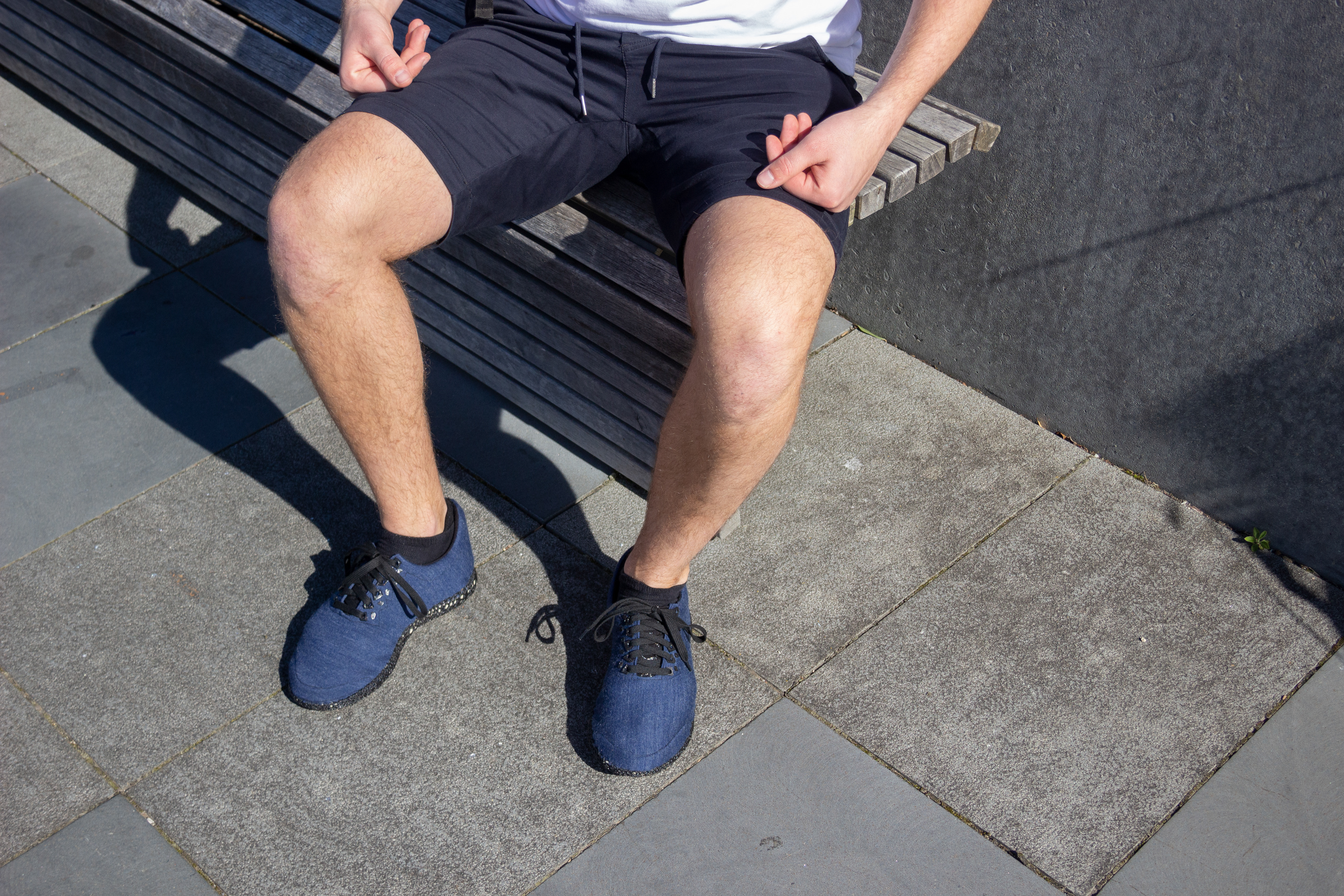